To: Motor Vehicle Corporation
I am a student at Rivendell high school and wish to submit an idea
for review. We have been studying forces and motion on the premise
of vehicular safety in our science class. Adam Stuart, and I (Ape-Iñago),
has elected the task of designing a new seatbelt system. To our
understanding, seatbelts work on the basic equation of F=ma (Force
= Mass x Accelleration). The idea is that since acceleration is
a factor of the change in distance / change in time, if we change
the time, it will decrease the force (see http://science.howstuffworks.com/fpte.htm).
So essentially, the more time the seatbelt takes to slow you down,
lower the acceleration will be. Since we are redesigning the whole
seatbelt, we wanted to focus on not only the amount of force it
creates, but also the comfort of the passengers. Seatbelts as they
are work fine, but we wanted to go with a different idea altogether;
by placing the “belt” onto a movable frame, all the
passengers can be hooked in with another seatbelt or even strapped
in with more solid device to distribute the force evenly. This design
works great with the newer Hydrogen Fuel-cell Cars that have their
engine near the wheels, since it leaves ample room for the seat
to move forward and backward (perhaps an ejection luggage compartment
in the back would help aswell).
We believe that having the belt hooked to a moveable seat, it will
allow the belt to be longer and thus make a bigger time of deceleration
and in the end less force on the passenger. Also, having the car
in a neutral position between two belts will also help stop the
whiplash effects since it will also bound backwards in the same
way (although it will need a system to prevent it from moving if
its not in a crash).
We have decided to test our theory on an egg in a seating system
set upon a Remote Control Car. In our tests, we will be looking
for a few variables that will effects the system. The first being
the speed of the car, because that will allow for the calculation
of the deceleration when hitting the wall. The next variable is
the weight of the entire system; more weight means a much higher
impact force. Another factor might be the “stretchiness”
of the rubber band (a substitute belt). And finally we’ll
need to actually calculate the force, and see how much it requires
to break the egg. I’ll explain how we measured these after
I describe the actual system:
We took an old remote control car (a red pt cruiser) and striped
it down to it’s bear essence. The front-end was chopped down
for weight. (for more speed). The rear axel was locked so it doesn’t
spin out. (Drives in straight line from start). We lengthened back
springs so it has more consistent traction. (More speed at take
off). Placed 2x200gm weights over back spring, with hot glue. (More
speed/straight line). Placed 3 eyehooks on each side so we can thread
with fishing line. (Follows straight line). The seat was attached
to the top of the car using some twisted metal wires. The seat was
an ingenious design by my classmate Adam Stuart. It was made out
of what he describes as cauterized steel. Using a pair of steel
tubes and two steel slabs, he made a track. On this track slides
a custom molded seat for the egg made out of “body putty”,
since it was the strongest material we could find to mold. The hollow
tubes contain a swivel like system that makes a pin drop out of
the sliding seat when the car hits the wall (as mentioned before,
we don’t want it swaying back and forth when not in an impact).
The car will be driven down a pair of taught fishing lines into
a solid wall. There is a piece of wood duct-taped to the wall at
the appropriate height so the collision will cause the metal rods
to move down the tube. These rods will make the dime spin and pull
the pin out of the seat. The removal of the pin allows the seat
to move forward and get the effects of the rubber band. Reference
the following diagram:
THE CAR:
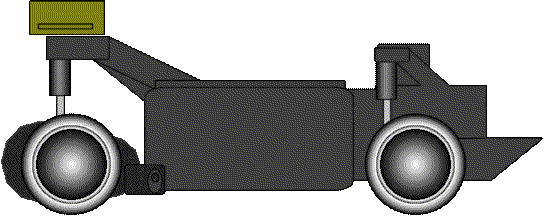
The Seat:
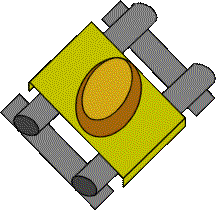
We calculated the speed by driving the car down the 10-meter stretch
of fishing line, and timed how long it took. It hit the end of the
line in 5.7077 seconds, so it had a speed of 1.752019202 meters
/second. The weight was a little tricky to get because the entire
vehicle was too heavy for an individual scale to measure, but we
balanced the car between 4 scales and then added them up, it weighed
a total of 1.64909kg including the battery which we weight separately.
The stretch ability of the rubber band we found using a simple method;
we hung a 200g weight on the end of a 2inch section, it stretched
2cm from its original position. At 400g on the same rubber band,
it stretched 4cm. And since gravity is a constant, you can figure
how much force was placed on the rubber band to stretch it that
far. Finally, the total force placed on the egg is equivalent to
50g * 1.752019202m/s, for a total of 0.0876009601g/m/s (Newtons).
After it was all set up, we proceeded to test our design with
hard boiled eggs. We did 21 runs, 11 with the safety system enabled,
and 10 with the seat immobile (we wedged the pin in so it wouldn’t
come out). Each run was done with the egg correctly positioned in
the seat and at the same distance from the wall (we had marked it
on the floor). For the 10 runs with the system engaged, the seat
moves forward a significant distance upon impact, and there is very
little done to the egg. There was a crack in the first of the test
eggs, but that was because we jammed it the seat a little too hard,
so we discarded those results from the safety system tests. The
10 runs without the safety system were a totally different story.
With the exception of one run, the egg would always fly out of the
seat and hit with the wall, so they all had quite significant dents
on the top of the shells. Also the part of the egg that was in contact
with the seat had a clear impact line coinciding with the location
of the seat’s ledge.
The system works, and is very effective. I’d venture to say
that it would be a much better way to have a belt in a car. It could
be designed relatively small, perhaps even placed in the area below
a car’s doors, and hooked onto the side of a thin mobile floor.
It alone would be as much, if not more effective then an ordinary
seat belt, since it allows for a much longer release of the force
from a collision.
Please Email Ape-Iñago (Ultimape@hotmail.com) with any responses
to this design, I’d be willing to answer questions. (and it
would make us feel proud to know its been looked at).
|